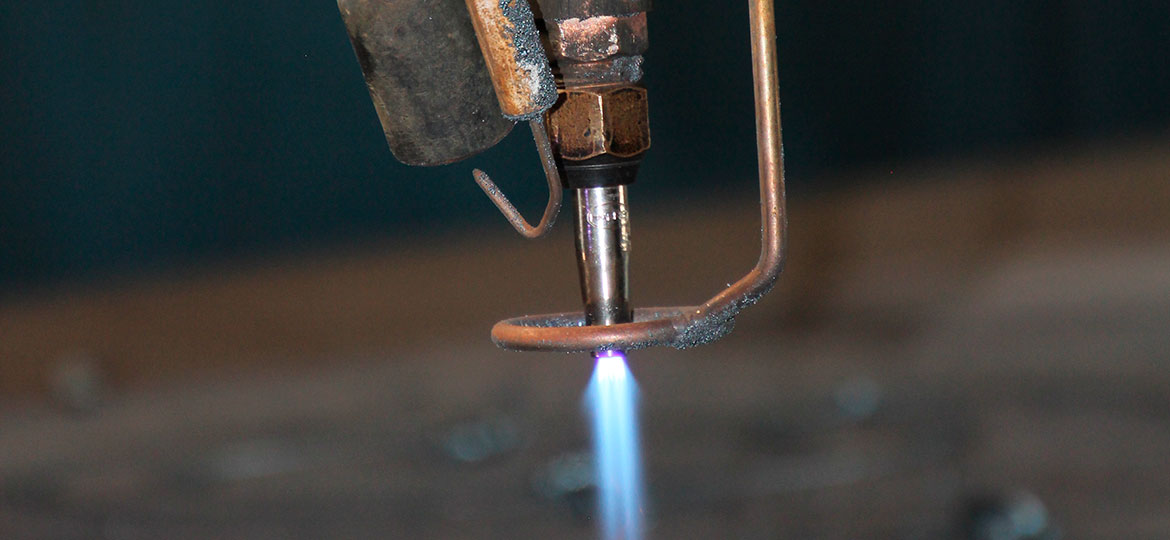
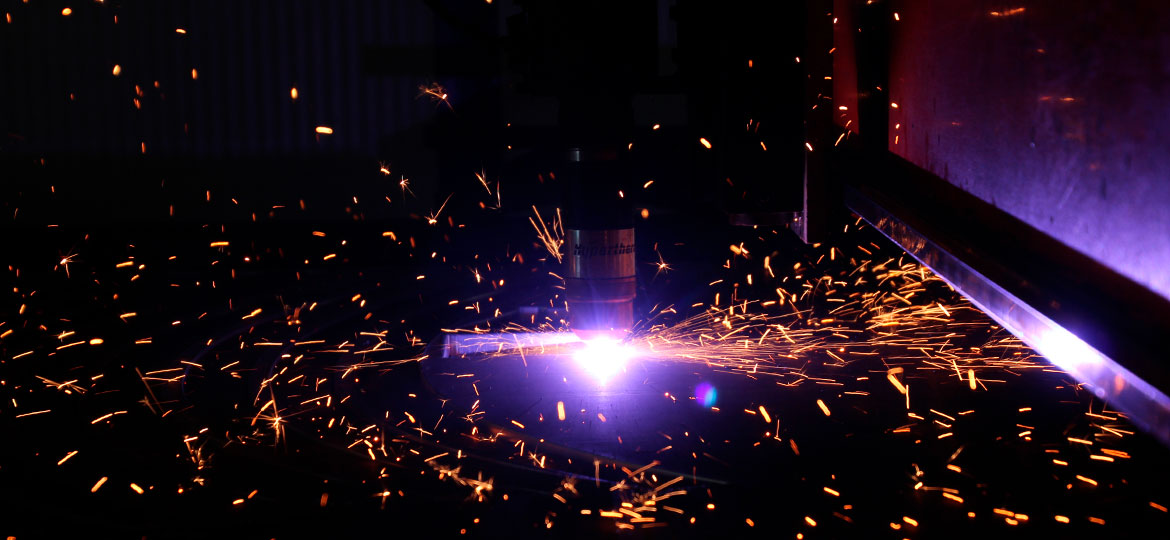
Plasma and Oxy
Using cutting machines, with plasma/oxyfuel technology very often happens to have to stop the cut for disparate reasons (change of consumables, torch shock on a cut piece, gas problems, etc.). The simplicity with which are managed these situations affects.
Oxy
- Management with on/off valves or proportionals
- Retral function on cutting losing with an only key
- Technological database
- Ramps of pressure on piercing/ cut >
- Moving piercings
- Automatic packaging
- Capacitive control gestion
- feedrate regulation cut with adjustment
- …. more
Plasma and drilling machines
- Multiple modes for the resumption of cutting, with attack automatic entry
- Control of cut height
- Technological database
- Gas automatic consolle gestion for the principal plasma operators
- Modify to the flight of cutting parameters
- Functions for trim sheet metal and manual cutting
- Radio
- Smokes aspiration with motorized or sector hood
- Tube cutting
- Drilling machines management with cycles of rigid tapping
- Functions for research and sheet realignment
- Feedrate regulation with flyer and more…
Plasma bevel
The use of a plasma to realize bevel processing is not a simple operation; anyone who has experience will concorde that is possible to get excellent results, provided you dedicate an important time in the gestion of corrections. For each material, for each spessor and also for type of cut (simple, negative simple, with shoulder, etc.) Compared to the historical straight cut, the bevel opens completely different scenarios: when you approach a new material, a different thickness proofs are needed to reach the desired result and all systems on the market expect to have to make the necessary corrections in the offline CAD/CAM programming system. Moreover, the electrode wear that normally involves simply a not optimal working height, in this case it leads to errors of dimensions, and in the case of shoulder processing the overcoming of the allowed tollerances. ECP1000 proposes a different approach, corrections are carried out in machine, availing of a powerful technological database and using a powerful geometric motor directly on the numerical control. Besides of obvious considerations about saving time from not having to act on CAD/CAM system is evident that this approach is more practical and efficient. Corrections are moreover saved in the technological database of CN and they will can be used successively to reset times of programming correction for the material/thickness used. Besides the relative corrections to startup settings is possible to correct automatically the program in the function of the real thickness of the material (this need due to the inevitable tolerances of the metal lamination). It is implemented moreover a function for the wear/misuration estimation of the electrode, in and the automatic resulting compensation. The correction function in machine requests the use of CutExpert as programming system.
LASER
The noble technology of the thermal break
The same hardware platform, some terminals of I/O Ethercat, a choice of motorization of quality (possibly with linear motors) and ECP1000 can be used to realize laser systems. The base functionality of the terminal cut are valid also for the laser cut besides a certain number of new cycles for:
- modulation on the fly of parameters PWM for the differentiated management
- modulation at the fly of PWM parameters for the differentiated version of the piercing parameters
- modulation on the fly of parameters PWM for the differentiated management
- modulation on the fly of parameters PWM for the differentiated management
- Flying cut
- special process gestion for pre-piercing, vaporization
- realtime control of cutting parameters
- realtime control of parameters of the laser source