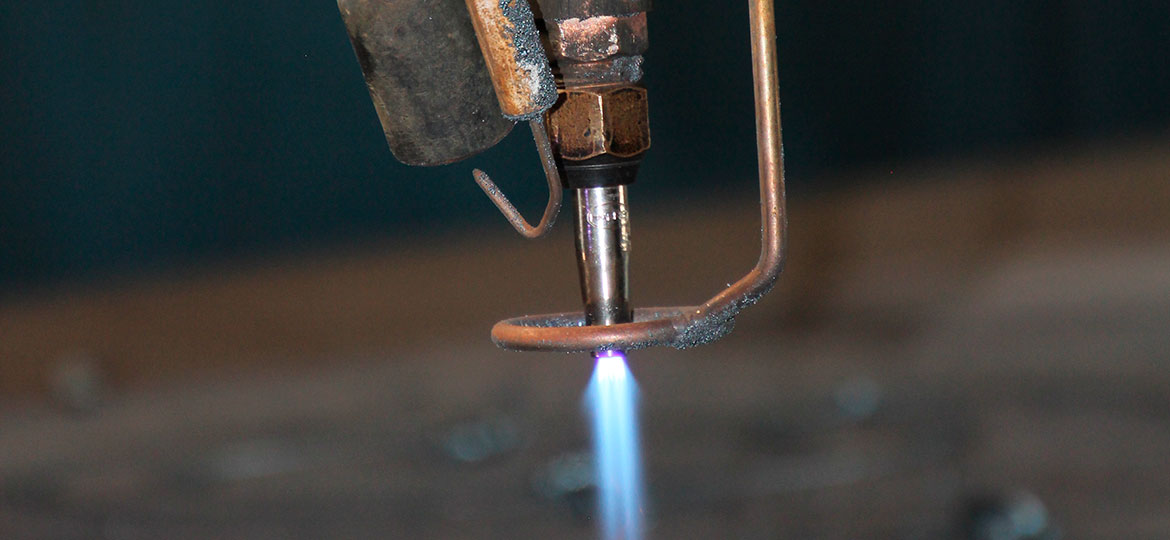
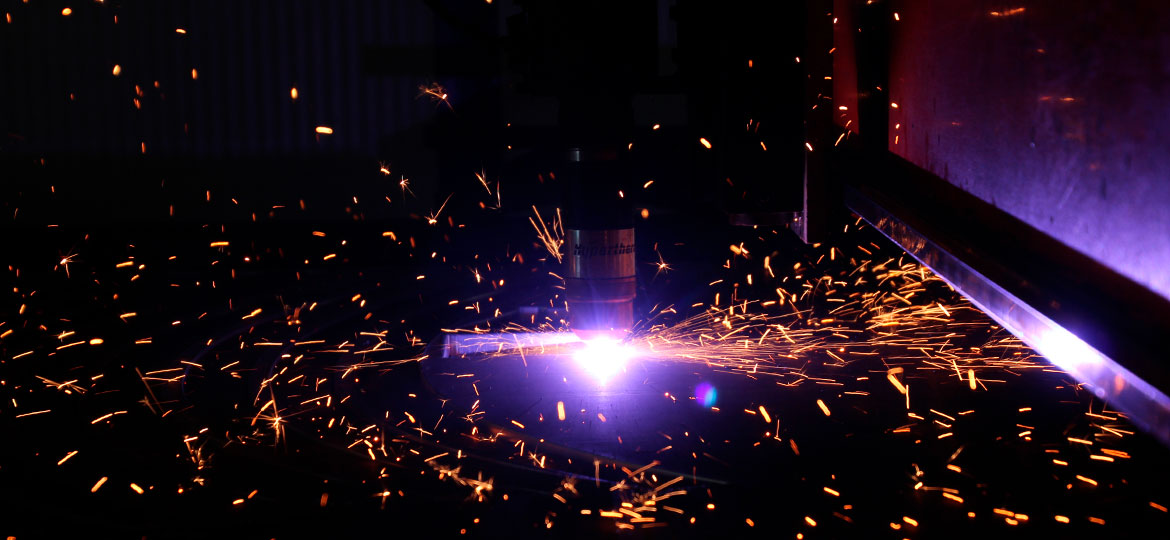
Plasma e Ossitaglio (Oxy)
Utilizzando macchine da taglio, con tecnologia plasma/ossitaglio (Oxy) molto spesso capita di dover interrompere il taglio per motivi disparati (cambio dei consumabili, urto della torcia su un pezzo tagliato, problemi con i gas, etc.). La semplicità con cui vengono gestite queste situazioni incide fortemente sulla percentuale dei fermi macchina e complessivamente sul grado di soddisfazione nell’utilizzo dell’impianto.
Ossitaglio (Oxy)
- Gestione con valvole on/off o proporzionali
- Funzione retrace su perdita del taglio con un solo tasto
- Database tecnologico
- Rampe di pressione su piercing / taglio
- Piercing in movimento
- Impacchettamento automatico
- Gestione controllo capacitivo
- Regolazione feedrate taglio con volantino
- .... molto altro
Plasma e foratrici
- Molteplici modalità per la ripresa del taglio, con inserimento automatico attacco
- Controllo di altezza taglio
- Database tecnologico
- Gestione gas consolle automatica per i principali generatori plasma
- Modifica al volo dei parametri di taglio
- Funzioni per rifilo lamiera e taglio manuale
- Radiocomando
- Aspirazione fumi con cappa motorizzata o a settori
- Taglio tubo
- Gestione foratrici con cicli di maschiatura rigida
- Funzioni per la ricerca e riallineamento lamiera
- Regolazione feedrate con volantino e molto altro...
Plasma Bevel
L’utilizzo di un plasma per realizzare lavorazioni Bevel non è una operazione semplice; chiunque abbia esperienza concorderà che è possibile ottenere risultati eccellenti, a patto di dedicare un tempo importante nella gestione delle correzioni.
Anche se si dispone di una meccanica perfetta, il processo di taglio plasma, al variare degli angoli e dei materiali è caratterizzato da differenti valori riguardo : larghezza di taglio, tensione di arco per mantenere una altezza ottimale, angolo di taglio effettivamente realizzato.
Per ogni materiale, per ogni spessore e anche per tipologia di taglio Bevel (semplice, semplice negativo, con spalla, etc.)
Rispetto allo storico taglio dritto, il Bevel apre scenari completamente diversi : quando si approccia un nuovo materiale, un diverso spessore occorrono prove su prove per raggiungere il risultato desiderato e tutti i sistemi in commercio prevedono di dover effettuare le correzioni necessarie nel sistema CAD/CAM di programmazione offline.
Inoltre, l’usura dell’elettrodo che normalmente comporta semplicemente una non ottimale altezza di lavoro, in questo caso porta a errori di dimensioni, e nel caso di lavorazioni di spalle il superamento delle tolleranze consentite.
ECP1000 propone un approccio diverso, le correzioni vengono effettuate in macchina, avvalendosi di un potente database tecnologico e utilizzando un potente motore geometrico direttamente sul controllo numerico.
Oltre a ovvie considerazioni riguardanti il risparmio di tempo derivante dal non dover agire sul sistema CAD/CAM è evidente che questo approccio è più pratico ed efficace.
Le correzioni vengono inoltre salvate nel database tecnologico del CN e potranno essere utilizzate successivamente per azzerare i tempi di correzione programma per il materiale / spessore utilizzato.
Oltre alle correzioni relative a settaggi di startup del processo è possibile correggere automaticamente il programma in funzione del reale spessore del materiale (esigenza questa dovuta alle inevitabili tolleranze della laminazione del metallo).
E’ implementata inoltre una funzione per la stima / misurazione dell’usura dell’elettrodo, in e la conseguente compensazione automatica.
La funzione di correzione in macchina richiede l’impiego di CutExpert come sistema di programmazione.
LASER
La tecnologia nobile del taglio terminco
La stessa piattaforma hardware, alcuni terminali di I/O Ethercat, una scelta di motorizzazione di qualità (possibilmente con motori lineari) ed ECP1000 può essere utilizzato per realizzare impianti laser. Le funzionalità base del taglio termico sono valide anche per il taglio laser oltre ad un certo numero di cicli nuovi per :
- modulazione al volo della potenza del laser in funzione della velocità
- modulazione al volo dei parametri PWM per la gestione differenziata delle fasi di piercing
- controllo pressioni gas mediante valvole proporzionali
- gestione integrata del controllo capacitivo
- taglio al volo
- gestione processi speciali per pre-piercing, vaporizzazione
- controllo realtime dei parametri di taglio
- controllo realtime dei parametri della sorgente laser